Waterproofing Solutions for Roof Decks and Balconies
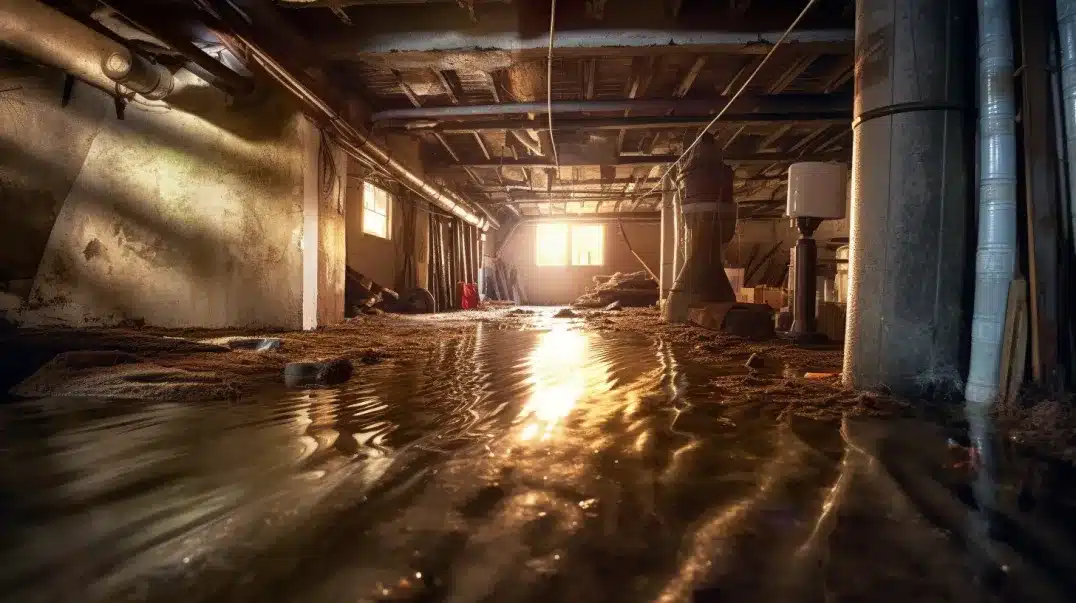
Outdoor living spaces serve as extensions of our homes, offering a tranquil escape into nature and a perfect venue for social gatherings, relaxation, and family activities. However, the exposure of these areas to the elements makes them vulnerable to various environmental impacts, particularly water damage. This underscores the need for effective waterproofing—a vital component not only to protect but also to enhance these cherished spaces.
In this blog, we delve into the significance of waterproofing for patios, decks, outdoor kitchens, and other external areas. Waterproofing these spaces is crucial for preserving the structural integrity and aesthetic appeal of materials exposed to moisture and adverse weather conditions. Without proper waterproofing, wood can rot, metals may corrode, and concrete could crack, leading to costly repairs and safety hazards.
Moreover, waterproofing outdoor living spaces ensures that their functionality and comfort are maintained year-round, protecting against unpredictable weather and extending the longevity of the investment made in creating these beautiful outdoor havens. Join us as we explore the innovative solutions and benefits of integrating waterproofing into your outdoor design strategy, ensuring that your outdoor living spaces remain durable, safe, and enjoyable for years to come.
Understanding the Need for Waterproofing in Outdoor Spaces
Exposure to Elements
Outdoor spaces like roof decks and balconies face continuous exposure to water, snow, and ice, each presenting unique challenges to the structural integrity of these areas. Water can seep into the smallest cracks and crevices, expanding as it freezes, which exacerbates the cracks and weakens the structure. Snow, accumulating over time, can exert significant weight on a structure, stressing materials and joints. Meanwhile, prolonged exposure to moisture without proper drainage or sealing can lead to the corrosion of metallic fixtures and the rotting of wooden elements.
The impact of climate variations also plays a critical role in the need for specialized waterproofing solutions. In areas with heavy rainfall or snow, waterproofing becomes a protective shield that extends the lifespan of building materials and maintains the structural health of the space. Conversely, in regions with fluctuating temperatures, waterproofing materials need to be flexible enough to expand and contract without cracking. Understanding these environmental impacts is crucial for selecting the right waterproofing techniques and materials that ensure durability and resilience.
Common Issues Due to Poor Waterproofing
Inadequate waterproofing can lead to a myriad of problems, starting with the most obvious: leaks. Leaks not only cause immediate discomfort but can also lead to more severe water damage, including the deterioration of both external and internal structural components. Over time, persistent moisture creates an ideal environment for mold and mildew, which pose serious health risks and can lead to costly remediation efforts.
The long-term consequences of neglecting waterproofing extend beyond repairs. Property value can plummet if waterproofing issues are not addressed, as potential buyers are less likely to invest in a property with known water damage. Furthermore, the usability of these outdoor spaces can be significantly reduced if they are frequently waterlogged or deteriorating, depriving owners of the full enjoyment and functional benefits of their investment.
Types of Waterproofing Materials for Roof Decks and Balconies
Liquid Waterproofing Membranes
Liquid waterproofing membranes, which include polyurethane, acrylic, and silicone-based solutions, offer a flexible and effective method for protecting roof decks and balconies from water penetration. These membranes are applied in liquid form and cure to form a seamless, impermeable barrier that conforms to the substrate. Polyurethane membranes are known for their durability and excellent water resistance, making them ideal for areas subjected to heavy foot traffic or standing water. Acrylic-based membranes, on the other hand, are UV resistant and more environmentally friendly, suitable for exposed areas that receive a lot of sunlight. Silicone-based membranes provide excellent longevity and weather resistance, handling extreme temperatures and UV exposure well.
The benefits of using liquid membranes include their adaptability to complex shapes and their ability to form continuous waterproof layers without joints or seams. However, their limitations include the need for professional application to ensure proper coverage and thickness, and their sensitivity to conditions during application, which can affect the curing process and final performance.
Sheet Membranes
Sheet membranes come in various types, such as bituminous and PVC options, each suitable for different waterproofing needs. Bituminous sheet membranes, often reinforced with fiberglass or polyester, are robust and have excellent tensile strength, making them ideal for areas that expect significant thermal movement or mechanical stress. PVC membranes, known for their flexibility and lightweight properties, are an excellent choice for projects where weight is a concern and where chemical resistance is necessary.
The installation of sheet membranes involves rolling out preformed sheets and bonding them to the substrate using adhesives or mechanical fasteners, followed by heat-welding or solvent-welding at the seams to create a continuous barrier. This method is most effective in scenarios where a quick and reliable installation is required, such as in large commercial projects or in residential applications with tight project timelines. The main advantages include their high resistance to punctures and tears, but they can be challenging to install in complex areas without creating overlaps or potential weak points.
Cementitious Waterproofing
Cementitious waterproofing materials consist of a mixture of cement, sand, and a specific type of water-reactive compound. This blend is applied to surfaces to create a rigid or semi-flexible type of waterproofing layer. It is best used in areas where a tough, durable barrier is needed, such as in underground parking structures or on concrete decks.
The pros of using cementitious materials include their ease of application and their compatibility with concrete surfaces, which makes them a practical choice for projects involving concrete repairs or overlays. They are also not reliant on weather conditions for curing, making them suitable for a wide range of climates. However, their inflexibility means they can be susceptible to cracking if the substrate moves or shifts significantly. Additionally, their aesthetic appeal is limited, often requiring overcoating or finishing treatments when used in visible areas.
Preparing for Waterproofing Installation
Surface Preparation
Preparing the surface of roof decks and balconies is a critical first step in the waterproofing process. This section of the blog will outline the necessary steps to ensure that the surface is ready for a waterproofing application. These steps include cleaning the area thoroughly to remove dirt, debris, and any existing coatings that may impair the adhesion of the new waterproofing materials. It is also crucial to repair any cracks or irregularities in the surface to prevent future water infiltration that could undermine the waterproofing system.
The importance of addressing these repairs before applying waterproofing materials cannot be overstated. Neglecting to fix underlying issues can lead to failures in the waterproofing layer, resulting in leaks and extensive water damage over time. This section will emphasize how proper surface preparation not only enhances the effectiveness of the waterproofing treatment but also extends the life of the structure by preventing issues before they start.
Drainage Considerations
Effective drainage is essential to the long-term success of any waterproofing system. This part of the blog will discuss how to ensure proper drainage on roof decks and balconies to prevent water accumulation, which can lead to structural damage and reduced effectiveness of the waterproofing material. Highlighting the importance of slope in the design of outdoor living spaces, this section will guide readers on incorporating slight inclinations to direct water towards designated drainage points.
Additionally, different drainage solutions that can be integrated into the waterproofing process will be explored. Options such as installing drainage mats under the waterproofing membrane, using drain grates, and incorporating scuppers for open balconies will be discussed. Each solution will be evaluated based on its suitability for different types of projects, providing readers with practical advice on choosing the right drainage strategy to complement their waterproofing efforts.
Best Practices for Waterproofing Roof Decks and Balconies
Choosing the Right Material
Selecting the appropriate waterproofing material is critical for ensuring the longevity and effectiveness of the waterproofing system on roof decks and balconies. This section will explore the key factors that must be considered when choosing waterproofing materials. These factors include exposure to elements such as sunlight, rain, and temperature fluctuations; the amount of foot traffic the area is expected to receive; and the aesthetic preferences that complement the overall design of the property.
We will provide practical tips for matching these materials to the specific needs of roof decks and balconies. For instance, areas with high exposure to sunlight may benefit from UV-resistant coatings, whereas high-traffic areas might require more durable materials like reinforced membranes or thicker coatings to withstand wear and tear. The discussion will guide readers through the process of evaluating their specific conditions and selecting a material that provides both protection and visual appeal.
Application Techniques
The success of a waterproofing project largely depends on the correct application of the chosen materials. This segment will serve as a detailed guide on how to apply different types of waterproofing materials effectively. For liquid membranes, we will discuss the importance of applying a uniform thickness across the surface and techniques for ensuring complete coverage around edges and corners. For sheet membranes, the focus will be on proper seam alignment and securement to prevent leaks.
Additionally, this section will address common pitfalls to avoid during the waterproofing application process. These include inadequate surface preparation, incorrect material mixing ratios, and insufficient curing times which can all compromise the integrity of the waterproofing layer. By highlighting these potential errors and how to avoid them, the blog aims to empower DIY enthusiasts and professionals alike with the knowledge to achieve a successful, long-lasting waterproofing job.
Maintenance and Care for Waterproofed Surfaces
Routine Inspection and Maintenance
Maintaining the integrity of waterproofed surfaces is crucial for extending their lifespan and ensuring they continue to protect structures from water damage effectively. This section of the blog will outline suggested maintenance routines that property owners can follow to keep their waterproofed areas in optimal condition. Regular inspection is key, with emphasis on checking these surfaces after extreme weather events such as heavy rains, snow, or prolonged exposure to high temperatures, which can accelerate wear and tear.
We will also discuss the signs of potential waterproofing failure, which include visible cracks, blistering of coatings, softening of membranes, water pooling, and the appearance of mold or mildew. Recognizing these early warning signs can prevent minor issues from escalating into major problems. Practical tips will be provided on how to address these signs, including proper cleaning methods, reapplying sealants, and patching small areas to prevent leaks.
Repair and Restoration
Over time, even well-maintained waterproofed surfaces may require repairs due to aging or unexpected damage. This part of the blog will guide readers on how to handle repairs on waterproofed roof decks and balconies effectively. It will include step-by-step instructions for common repair techniques such as resealing joints, replacing damaged sections of a membrane, and applying patching compounds to cracks.
Additionally, it’s crucial to know when to call a professional for help. This section will advise on situations where professional intervention is recommended, such as when dealing with structural damage, extensive water infiltration, or when the original waterproofing system fails to meet performance expectations. Tips on selecting a qualified contractor and what to expect during the repair process will also be provided, ensuring that readers are equipped to make informed decisions about managing and restoring their waterproofed surfaces.